Description
● High efficiency, every minute can weld 15 - 20 studs
● Pretty weld appearance, without further processing
● Welding cable may be extended up to 20 meters, without affecting the welding.
● Easy to operate, convenient and easy to study.
● The pipe heat insulation stud welder are available,which the stud torch is different from the ship insulation stud welder.
Specifiction
Model | Insulation Nail Welder |
Welding Current Output Mode | Capacitor Discharge |
Capacitor Specifications (μF) | 99,000 |
Welding Speed (pc/min) | 15-20pcs/min |
Working Voltage(V) | 30-198V |
Input Power Voltage(V) | 220V |
Frequency(Hz) | 50/60 Hz |
Applicable range of the thickness for the plate | 1-20mm |
Welding Diameter (mm) | 3-4mm |
Dimension((mm) | 440×340×160 |
Weight(Kg) | 24 |
Type of the welding torch | Electrode holders type |
Application: Stud welding has become the standard in many fastening applications in industrial and commercial buildings, bridges, power generating structures, military vehicles, automobiles, trucks and off-road equipment. Stud welding literally anchors other components to the basic framework of structures without piercing the basic framework and provides superior strength to traditional welding methods.
Moreover, stud welding is much faster than hand welding and does away with all the problems inherent with holes in structural members.
Advantages of the stud welding:
No Need for Holes: |
eliminates cost of making them -- or of sealing them |
Lower Failure Incidence : |
no holes eliminates risk associated with leakage, corrosion and damage |
Superior Strength: |
greater than that of base metal |
Faster Installation: |
than comparable one-sided fasteners (sometimes as much as 4x faster!) |
No Distortion/Blemishes: |
other side needs no treatment |
Total Flexibility: |
weld studs anywhere, at any time |
Design Freedom: |
improved appearance, no exposed fasteners |
Lowest In-place Cost: |
the natural result of all the above! |
Process:Stud welding involves the same basic principles and metallurgical aspects as any other type of arc welding procedure — a controlled electric arc is used to melt the end of a stud or electrode and a portion of the base metal to form a bond. The stud is plunged automatically into the molten metal and a high quality fusion weld is made where the weld is stronger than the stud itself. A variety of metals can be used in stud welding, however, the more common types include mild steel, stainless steel and aluminum.
Dependent upon the type of application, studs may be fed into the welding gun automatically or manually. In either case, a simple squeeze of the trigger produces a positive attachment in a split second. Stud weld fasteners may be most any size, shape or type and there are literally hundreds of types available. However, the stud material must be weldable and one end of the stud must be designed for welding. While conventional DC welding machines may be used, special power units designed specifically for high-strength fastening are recommended.
There are three primary types of stud welding processes –Capacitor discharge, electric arc, and gas arc.
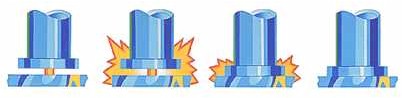
Short Cycle and Gas Arc processes both offer ferrule-less stud welding. The short cycle process uses studs that do not have flux loads and have blunt weld ends and flange diameters slightly larger than the studs’ diameter to facilitate auto feeding and assure weld strength. Short cycle systems are typically mounted on robots in automotive plants requiring high productivity, but can also be used for low volume hand gun applications. The gas arc process utilizes gas shielding in place of ceramic ferrules to protect the weld metal and arc. Gas can be used to weld mild steel, stainless and aluminum studs up to 3/8" diameter. The process is used extensively to weld studs to aluminum pots and pans for securing handles and legs.
BORTE engineering professionals will work with you to determine the type of welding process that best meets your application’s design criteria. In addition to numerous stud types, we also offers a full line of fasteners and stud welding equipment to perform all of the processes described above.